The Key Factors That Enhance Corrosion Resistance in Electroless Nickel Plating
In industries requiring long-lasting protection against harsh environments, electroless nickel plating equipment offers superior corrosion resistance for a wide range of applications. As a crucial part of surface treatment solutions, this plating method ensures uniform coverage, extending the life of components in industries like automotive, aerospace, and chemical processing. This article will break down the five critical aspects that contribute to the corrosion resistance of electroless nickel plating, giving you a deeper understanding of how this technology can benefit your operations.
Table of contents
Phosphorus Content: The Foundation of Corrosion Resistance
Environmental Suitability: Tailored Solutions for Harsh Conditions
Uniform Surface Finish: Coverage Without Compromise
Thickness of the Coating: More is More
Heat Treatment: Enhancing Performance Post-Plating
Phosphorus Content: The Foundation of Corrosion Resistance
The level of phosphorus in the nickel plating is one of the primary determinants of corrosion resistance. High-phosphorus electroless nickel plating (10-12% phosphorus) provides excellent protection, particularly in acidic or saline environments. The phosphorus reacts with the nickel to create a coating that is both highly uniform and resistant to corrosive attacks, ideal for applications in industries exposed to chemicals or saltwater environments. Low-phosphorus coatings, on the other hand, are better suited for alkaline conditions, offering greater abrasion resistance but lower corrosion protection. For industries dealing with extreme corrosion, high-phosphorus coatings are the optimal choice, ensuring durability and long-lasting protection.
Environmental Suitability: Tailored Solutions for Harsh Conditions
Different environments demand different levels of protection, and electroless nickel plating adapts to a variety of challenging conditions. From marine applications to chemical processing, this technology provides resistance to a wide range of environmental factors, including salt spray, acids, and caustic solutions. This adaptability makes it a preferred choice in industries where corrosion can lead to rapid degradation of components, such as in offshore drilling or chemical plants. The ability of electroless nickel plating to endure harsh environments without sacrificing performance is a critical reason for its widespread adoption across multiple industries.
Uniform Surface Finish: Coverage Without Compromise
One of the standout features of electroless nickel plating equipment is its ability to deposit a uniform coating across even the most complex geometries. Unlike traditional electroplating, electroless nickel plating does not rely on an external electrical current, meaning it can coat surfaces uniformly, regardless of shape. This results in enhanced corrosion protection, as every part of the component—whether flat, curved, or intricately detailed—receives the same level of protection. In environments where corrosion can attack hidden or hard-to-reach areas, this uniform coating is a significant advantage.
Thickness of the Coating: More is More
The thickness of the electroless nickel layer is another factor that influences corrosion resistance. Thicker coatings provide more robust protection, ensuring that components exposed to extreme corrosive environments have a longer operational life. For applications requiring extended periods of exposure to harsh chemicals or outdoor elements, increasing the thickness of the nickel layer offers a more effective barrier, preventing corrosive elements from reaching the substrate. This makes it ideal for use in demanding industries like aerospace or oil and gas, where the longevity and integrity of components are critical to safety and performance.
Heat Treatment: Enhancing Performance Post-Plating
Post-plating heat treatments play a crucial role in improving the mechanical properties of the coating, further enhancing corrosion resistance. After plating, components are often heat-treated to increase the hardness and adhesion of the nickel layer, creating a more durable and long-lasting surface. This process is especially important for industries where components are exposed to both high temperatures and corrosive environments, such as in automotive engines or industrial furnaces. By enhancing the bond between the nickel and the substrate, heat treatment reduces the risk of flaking or delamination, ensuring that the corrosion-resistant properties of the coating are maintained over time.
Electroless nickel plating offers unparalleled corrosion resistance, making it a go-to solution for industries that require durable, long-lasting surface treatments. By understanding the role of phosphorus content, environmental suitability, uniform surface coverage, coating thickness, and heat treatment, businesses can optimize their surface treatment processes to ensure maximum protection and performance. If you are interested in learning more about how electroless nickel plating can benefit your business, visit Fengfan's website to explore their range of surface treatment equipment designed for superior results.
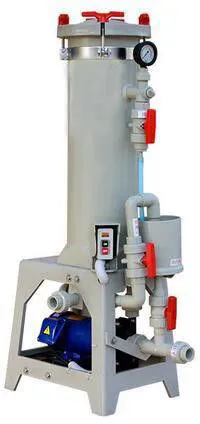
Comments
Post a Comment