Innovations and Trends in Plate and Shell Heat Exchanger Technology
Plate and shell heat exchangers have long been a cornerstone of industrial processes requiring efficient thermal management solutions. With advancements in technology and increasing demand for more sustainable and robust systems, manufacturers, such as ACME, are pushing the boundaries of what these devices can achieve. Combining precision engineering with cutting-edge materials, plate and shell heat exchangers are evolving to meet the diverse needs of industries such as petrochemicals, pharmaceuticals, food processing, and HVAC.
Table of contents:
How Advanced Manufacturing Improves Heat Exchanger Durability and Efficiency
The Role of Plate and Shell Heat Exchangers in High-Temperature Applications
How Modular Designs Are Transforming Heat Exchanger Flexibility
This article explores key innovations, applications, and trends in this sector, offering insights for businesses looking to enhance operational efficiency with the latest developments in heat exchanger technology.
How Advanced Manufacturing Improves Heat Exchanger Durability and Efficiency
Advancements in manufacturing processes have significantly bolstered the durability and efficiency of plate and shell heat exchangers. Innovations in laser welding techniques have enabled manufacturers to create more robust and compact designs without compromising performance. Laser-welded plate assemblies are replacing traditional tubular elements, incorporating corrugated plates designed to improve heat transfer rates while minimizing energy loss. These designs are particularly effective in handling high-pressure applications and operating in extreme temperatures, making them a versatile solution for demanding industrial environments. Materials innovation also plays a crucial role in this evolution. Manufacturers are increasingly utilizing corrosion-resistant alloys and composite materials to prolong the life span of heat exchangers. These materials ensure resilience against chemical exposure and temperature fluctuations, reducing long-term maintenance costs while enhancing reliability. ACME stands as a primary proponent of these technologies, offering durable, efficient heat transfer solutions tailored for specialized industrial applications.
The Role of Plate and Shell Heat Exchangers in High-Temperature Applications
One of the most vital functionalities of plate and shell heat exchangers is their capability to handle high-temperature and high-pressure conditions. Thanks to their all-welded, gasket-free designs, these exchangers exhibit superior strength, ensuring safe and effective operation in extreme environments. This high-grade construction makes them an excellent choice for applications such as power generation, chemical processing, and pharmaceuticals, where operational stability under challenging conditions is critical. Unlike traditional shell-and-tube exchangers, the laser-welded plate assemblies in plate and shell designs allow for superior heat transfer performance. The corrugated plates maximize surface contact between the media, enabling efficient thermal exchange even in processes requiring rapid temperature shifts or differing thermal properties between fluids. The smaller temperature differentials also reduce the risk of fouling, ensuring operational efficiency over time. Industries such as petrochemicals and HVAC systems particularly benefit from this innovation by reducing downtime and improving the overall performance of their heat transfer systems. ACME, a leading plate and shell heat exchanger manufacturer, provides customizable solutions for high-temperature applications, assisting businesses in overcoming their thermal management challenges with reliable, efficient heat transfer technology.
How Modular Designs Are Transforming Heat Exchanger Flexibility
Modular heat exchanger designs are another exciting trend revolutionizing this field. With standard systems often struggling to meet the diverse operational requirements of modern industries, modular systems allow for unprecedented flexibility. Businesses can expand or modify their heat exchangers based on process changes without requiring a complete overhaul. This adaptability not only optimizes expenditure but also mitigates the challenges associated with rapid technological or process changes in industrial environments. Modular construction breaks the heat exchanger into manageable sections, making transportation, installation, and maintenance more accessible. Each module can be adjusted individually, simplifying customization for specific applications or industries. Whether it's extending the heat exchanger’s operational capacity or updating individual system components to accommodate new performance standards, modular systems make upgrades seamless and cost-effective.
Smart industrial organizations are increasingly turning to advanced heat transfer technology to enhance operational efficiency, reduce costs, and meet the demands of sustainable production. With innovations such as advanced manufacturing processes, superior performance in high-temperature applications, and the flexibility offered by modular designs, plate and shell heat exchangers are setting new industry benchmarks. Businesses partnering with trusted providers like ACME not only gain access to cutting-edge solutions but also receive tailored support to meet specific operational needs, ensuring maximum performance and durability. For companies looking to enhance their thermal systems, adopting the latest plate and shell heat exchanger technology is a step toward achieving higher efficiency and long-term sustainability.
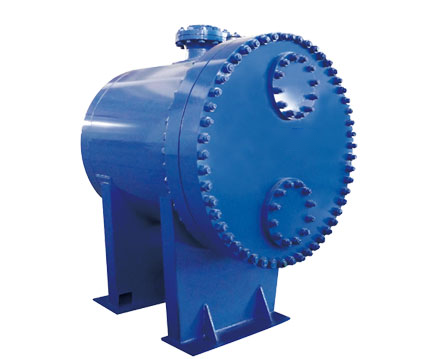
Comments
Post a Comment