PMI Foam for Sandwich Structures
Table of contents:
Sandwich Panel Applications Across Marine and Auto Industries
How PMI Foam Enhances Structural Integrity and Load Bearing
Designing Efficient Sandwich Composites with PMI Foam
Sandwich Panel Applications Across Marine and Auto Industries
PMI foam manufacturers continually innovate to meet the evolving needs of sectors like marine and automotive industries. These industries often require lightweight components for improved fuel efficiency and better overall performance. Sandwich structures made with PMI foam are used for creating hulls in high-speed boats, decks, bulkheads, and interior panels that demand moisture resistance and durability. Similarly, in the automotive domain, PMI foam enhances crashworthiness and reduces weight in vehicle body panels, dashboards, and structural elements. Its thermal and acoustic insulation capabilities also contribute to quieter and more energy-efficient vehicles.When employed in marine and auto designs, PMI foam ensures longevity and reliability by maintaining its integrity under adverse conditions, such as high humidity or extreme temperatures. Additionally, its closed-cell structure prevents water ingress, making it highly suitable for marine applications where consistent exposure to water is common.
How PMI Foam Enhances Structural Integrity and Load Bearing
The distinguishing feature of PMI foam lies in its ability to significantly enhance the structural integrity of sandwich composites. Its excellent compressive strength and rigidity provide a strong foundation for lightweight designs while allowing superior load-bearing capacity. Various grades of PMI foam, such as Rifeng PMI foam, offer tailored densities to meet the needs of different design requirements. For aerospace-grade projects, for example, PMI aerospace foams deliver exceptional performance under extreme stress, making them ideal for aircraft fuselage panels, wing sections, and rotor blades.PMI structural foam is known for its compatibility with processes like thermal molding and CNC machining. This versatility allows it to take on complex geometries without compromising on performance. The lightweight nature of PMI foam also means that resin infiltration is minimized during production, reducing unnecessary weight and maximizing core efficiency. Its superior dielectric properties further make it an excellent choice for applications like radomes and electronics that require functionality under electromagnetic conditions.
Designing Efficient Sandwich Composites with PMI Foam
The success of any sandwich structure design depends on the right choice of core materials, and PMI foam excels in this regard. Its adaptability to high-temperature curing processes, such as RTM (Resin Transfer Molding) and VARTM (Vacuum-Assisted Resin Transfer Molding), ensures efficient manufacturing without compromising quality. PMI foams such as Rifeng WH can endure curing temperatures up to 180°C, making them ideal for high-tech production environments.Designing with PMI foam also allows engineers to incorporate custom configurations to suit specific needs. Whether for aerospace, automotive, or industrial applications, customizable densities and shapes ensure precision in design. For example, pre-formed PMI foam cores can be directly integrated into products, saving time and resources during manufacturing. This efficiency, combined with the foam’s lightweight structure and robust performance, significantly improves ROI (return on investment) for end users across multiple industries.
PMI foam has revolutionized modern manufacturing with its unmatched combination of strength, durability, and low weight. Its adaptability to various applications, from aerospace to industrial settings, has demonstrated its significant value in reducing costs while maintaining performance standards. By integrating customizable configurations, businesses can achieve greater efficiency and sustainability in their production processes. As industries continue to innovate and demand higher-performing materials, PMI foam has emerged as a standout solution for addressing these challenges. Known for its exceptional strength-to-weight ratio, thermal stability, and versatility, PMI foam is widely used in applications ranging from aerospace and automotive to wind energy and advanced composites. Its ability to enhance performance while reducing weight makes it an indispensable material in cutting-edge manufacturing and engineering.
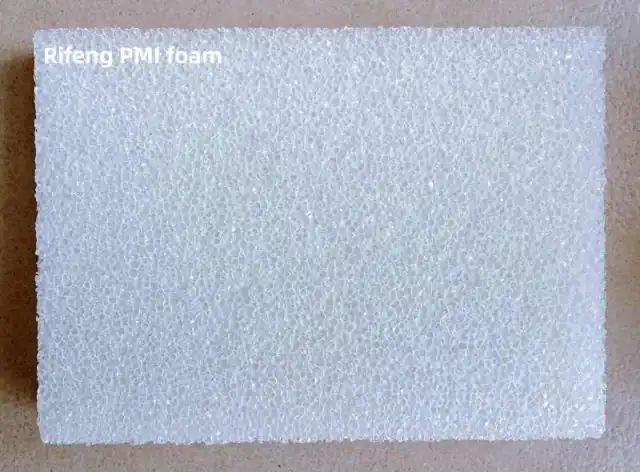
Comments
Post a Comment