Inside the Manufacturing Process How Filter Cartridge Manufacturers Ensure High Quality
Table of contents:
Multi-Layer Sintered Mesh Technology Explained
In-House Testing Procedures for Stainless Steel Filters
Tailoring Filtration Precision for Industrial Clients
Multi-Layer Sintered Mesh Technology Explained
Multi-layer sintered mesh technology forms the backbone of many stainless steel filter cartridges. At its core, this process involves stacking layers of stainless steel wire mesh, which are then vacuum sintered to create a unified structure. Each layer in this five-layer mesh design serves a distinct role: from the protective layer that safeguards against harsh environments, to the filtering layer designed for precise particle retention, and the supporting skeleton layers that provide stability and compressive strength. The result is a filter cartridge with exceptional properties, including highly uniform filtration accuracy ranging from 1 to 200 microns, ensuring precise and reliable performance across a wide range of applications. It also offers excellent permeability, allowing for efficient flow rates without compromising filtration quality, and demonstrates remarkable resilience in extreme temperature conditions, withstanding a range from -200 to 650 degrees Fahrenheit. These features make the cartridges ideal for demanding applications across various industries, including petroleum refining, where they handle harsh chemicals and high temperatures.
In-House Testing Procedures for Stainless Steel Filters
Manufacturers employ rigorous in-house testing to maintain the quality and reliability of stainless steel filter cartridges. Tests often involve assessing the filter’s mechanical strength, permeability, and corrosion resistance. For example, pressure differential tests are conducted to evaluate how the filter withstands operational stresses. Additionally, manufacturers test for uniformity in filtration performance to ensure consistent results across units. Another crucial component is backwash-ability testing, which assesses how easily the filter can be cleaned and reused. By prioritizing these quality checks, manufacturers guarantee that every stainless steel filter cartridge leaving their facility can perform seamlessly in demanding industrial environments.Companies within the filter element store ecosystem, such as SenjiaFilter, prioritize adhering to strict industry certifications, ensuring their products meet the highest standards of quality and safety. This commitment not only reflects their dedication to compliance but also highlights their focus on delivering reliable, efficient, and durable products that customers can trust for a variety of applications. By maintaining rigorous quality control and staying updated with evolving certification requirements, these companies continue to set benchmarks in the industry.
Tailoring Filtration Precision for Industrial Clients
Not all filters are created equal, especially when it comes to catering to the niche needs of diverse industries. To offer tailored solutions, filter cartridge manufacturers factor in specific client requirements such as flow rate, operating pressure, and particle retention efficiency. Whether it’s a custom interface design like a 222, 220, or 226 connector, or threaded and flange-specific options, customization plays a key role. For instance, clients in the chemical fiber industry may require filters specifically optimized for high-temperature tolerance to withstand the extreme heat generated during production processes. On the other hand, clients in the water treatment sector often prioritize filters with strong anti-corrosion properties to handle prolonged exposure to water, chemicals, and other potentially corrosive substances. This level of adaptability allows ss sintered filter cartridges to be customized to meet the unique demands of various industries, ensuring they are not only highly effective at filtration but also durable and perfectly suited for their intended applications. By catering to these specific needs, these filters deliver reliable performance and long-lasting value in even the most challenging environments.
Sintered stainless steel filter cartridges stand out as a reliable, durable, and highly adaptable solution for a wide range of industrial filtration needs. Their ability to withstand extreme conditions, combined with customization options to suit specific applications, ensures optimal performance and long-term value. By choosing these filters, industries can achieve enhanced efficiency, lower maintenance demands, and superior filtration results, solidifying their position as an indispensable component in modern filtration systems.
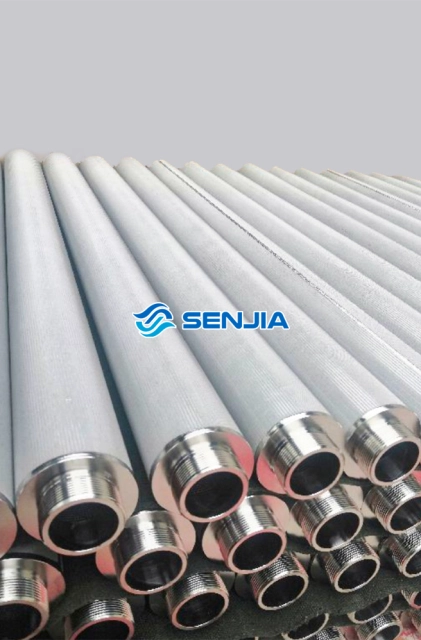
Comments
Post a Comment