Streamlining Your Vacuum Flask Line: The Power of Triple Stations CNC Technology
Table of contents:
Key Benefits of Implementing a Triple Stations CNC Spinning Neck Machine
Enhancing Product Quality Through Precision Spinning Neck Processes
Cost-Efficiency Analysis: Triple Stations vs. Traditional Spinning Methods
Adapting Your Production Line for the Triple Stations CNC Spinning Neck Machine
Key Benefits of Implementing a Triple Stations CNC Spinning Neck Machine
The Triple Stations CNC Spinning Neck Machine, developed by renowned spinning necking machine manufacturers, offers a multitude of advantages for vacuum flask production. This state-of-the-art equipment utilizes CNC and servo control systems to ensure precise operation, resulting in consistently high-quality outputs. The machine's robust construction, featuring cast iron sliding tables, provides the stability necessary for accurate spinning neck processes. With its user-friendly HMI interface and the potential for integration with robotic arms, this wholesale spinning necking machine paves the way for unmanned production, significantly boosting operational efficiency and reducing labor costs.
Enhancing Product Quality Through Precision Spinning Neck Processes
Quality is the cornerstone of successful vacuum flask production, and the Triple Stations CNC Spinning Neck Machine excels in this aspect. Designed by expert spinning necking machine manufacturers, this advanced machinery offers unparalleled precision and accuracy in the rotary compression of cup and pot necks. The vertical spinning design not only facilitates easier loading and unloading but also ensures a smoother finish on both straight pipes and pyramid-like structures. By implementing this wholesale spinning necking machine, manufacturers can achieve superior product quality, meeting and exceeding customer expectations in an increasingly competitive market.
Cost-Efficiency Analysis: Triple Stations vs. Traditional Spinning Methods
When considering the adoption of new technology, cost-efficiency is a crucial factor. The Triple Stations CNC Spinning Neck Machine, available from leading spinning necking machine manufacturers, offers a compelling case for investment. With its ability to process 2300-2500 pieces in an 8-hour shift, this wholesale spinning necking machine significantly outperforms traditional spinning methods. The increased productivity, combined with reduced labor requirements and improved quality control, results in a lower cost per unit. Moreover, the versatility of the machine, capable of handling working pipe diameters from 40-180mm and thicknesses of 0.25-0.8mm, allows manufacturers to streamline their production lines and reduce the need for multiple specialized machines.
Adapting Your Production Line for the Triple Stations CNC Spinning Neck Machine
Integrating the Triple Stations CNC Spinning Neck Machine into existing production lines is a strategic move for vacuum flask manufacturers looking to stay ahead of the curve. This wholesale spinning necking machine, crafted by industry-leading spinning necking machine manufacturers, is designed for seamless integration. Its compact size of 1600x1200x2745mm allows for efficient use of factory floor space. The machine's compatibility with robotic arms opens up possibilities for fully automated production lines, further enhancing efficiency and consistency. By partnering with experienced spinning necking machine manufacturers, companies can ensure a smooth transition and maximize the benefits of this advanced technology.
In conclusion, the Triple Stations CNC Spinning Neck Machine represents a significant leap forward in vacuum flask manufacturing technology. This innovative solution, offered by premier spinning necking machine manufacturers, addresses the industry's growing demands for precision, efficiency, and quality. By implementing this wholesale spinning necking machine, manufacturers can streamline their production processes, enhance product quality, and gain a competitive edge in the market. As the vacuum flask industry continues to evolve, embracing such cutting-edge technologies will be crucial for manufacturers aiming to meet customer demands and drive business growth in an increasingly competitive landscape.
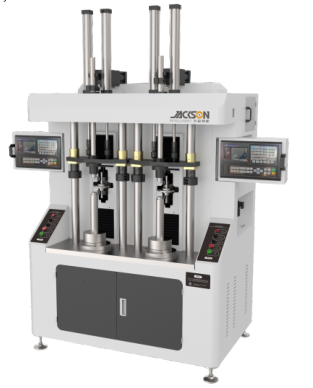
Comments
Post a Comment